Background of the technology transfer failure at Kamaishi iron mill
Hideki ONODERA
In Japan, from the last stage of Edo era, introduction of western technology was performed thick and fast. However, the failure example of many technology transfers are also included in these. This paper considers the cause of failure of the national Kamaishi iron mill, which was the greatest failure at that time. Lack of the iron demand accompanying with lacked market research, the Kamaishi iron mill generated a large amount of deficit. It was simplest way to avoid another deficit, that stopping operation immediately, engineer throw in raw ore into the furnace under operation, to make it blockade, in order to prevent pointing out the carelessness of preliminary survey, moreover, and to have laid on physical failure. This blockade of furnace was secondary factor as discontinuance of business, but there was a big meaning. Furthermore, this was useful to mitigation of the initial risk of the following private enterprise, which succeeded management, and had big influence when Japanese key industry growing up.
Key Words: technology transfer, failure, political reason, Kamaishi iron
mill
|
1. Introduction
In case of technology transfer to developing country, problems as large difference of the technical background of the area and/or the transfer technical level, difference of the expectation for partner, etc. derive failure of technology transfer. As a problem of Japanese engineer who performs technical instruction in developing country, (1) ignoring the actual condition of developing country, and forced the Japanese way. (2) Japanese or his common sense is made into the measure for all things. (3) cannot operate the apparatus unless who had used it before, are listed(1). And when a small number of foreign engineer commands a big project, also lack of management ability must become a case of fatal problem. Sometimes, failures owing to these problems are reported privately in a organization, however, it is rare to notice the reason to the exterior of the organization. Therefore, real reason of the failure normally hide behind a reason for being satisfactory. And in many cases, it is also rare that the reason of the failure applied for avoid another failure. In Japan, after the last several years of Edo era (1860-), rapid transfer and promotion of western technology were performed. Although some examples of failure on many area of technology transfer are contained. In almost cases, cause of failures are (1) or (2) mentioned above, and some of these kind of failure might be happen even in today. This paper presents the history from the foundation to the end of the national Kamaishi iron mill which was the most serious failure in technology transfer at the beginning of Meiji era.
2. Technical innovation of iron-manufacture around Kamaishi area
As shown in Table 1, the history of technical innovation of iron-manufacture around Kamaishi area, could be roughly divide at three terms(2).
Table 1 History of innovation of iron manufacture around Kamaishi

The 1st term is the time of the modernization from the bottom (inner side of the community) represented by conversion to the modern western style blast furnace from ancient "Tatara" iron industry. It starts in the foundation of the first full-scale iron industry in Japan by the western style blast furnace at Ohashi of western Kamaishi region by OSHIMA Takato in 1857, and finishes with abolition of the Hashino No. 3 blast furnace (life size model in a museum is shown in Figure 1) in 1894.

Fig. 1 Life size model of Hashino No.3 blast furnace.
The iron mine and industry around the Kamaishi area were modernized with instruction by OSHIMA. And finally, at the Kamaishi region, 12 of 14 set of the blast furnace all over Japan are existed. Therefore, domestic frontier full-scale industrial complex was founded at the district of north Tohoku area. Figure 2 shows the schematic of Ohashi blast furnace, and Fig.3 shows the distribution of modern blast furnaces, which were built until 1885. The numbers inside the parenthesis in the figure denotes the number of blast furnaces, respectively.

Fig. 2 Schematic of Ohashi blast furnace. | 
Fig. 3 Distribution of modern blast furnaces in Japan built until 1885. |
The 2nd term is the time of transfer of latest technology by the foreign employee at the national Kamaishi iron-mill installed by the Meiji Japanese government, and in another way of speaking, modernization from the top, which based on the "promotion of industry policy". However, this investment was not a demand from iron industry company who already existed, or the social and/or the environmental request, even if this modernization accompanied with a large amount of plant and equipment. Therefore, this iron-mill abolished in about only three years, based on the bad condition of operation and mistaken information on drain of iron ore stone resources, without taking into consideration the method of material supply from other area.
Then, when operation by the private Tanaka iron mill was started the 3rd term. In a profits pursuit policy in private enterprise, the modernization from inside was promoted again. Head YOKOYAMA Kyutaro and Engineer TAKAHASHI Matasuke built the newly OSHIMA type blast furnace of same scale, and October 16 in 1886, they succeed the continuous operation. The large 25t blast furnace of former national iron-mill was restored by Dr. NORO Kageyoshi and other Japanese engineers and re-operated successfully in 1893. He studied at University of Tokyo and studied mining at London University after graduation. By this way, the iron-manufacture system which was going to transfer from British employee and which went failure, was completed by the Japanese engineer, who finally found out the know-how by themselves.
3. Cause of failure of national iron-mill
The national blast furnace (Figure 4) started operation on September 13, 1880 and capability of iron was 7t per day. However, fire broke out in the charcoal manufacture factory on December 9, and since 15 warehouses were burned down and supply of the charcoal for furnace fuel (reducing agent) became impossible, iron manufacture was stopped on the 15 of December. The quantity of the pig-iron produced by operation for these 97 days is 3,324,974 lb (about 1500t), and when it is averaged, it is 15t per day.
However, another fire broke out in another charcoal manufacture place of Oh-matsukurayama on May 15, 1881, and fire spread on the neighboring mountain, finally the 20,000 trees were burned down and area burned down at this time was about 170ha. Therefore, it had to stop the operation of blast furnace for about one year for these accidents(3).

Fig. 4 National 25t blast furnaces.
Iron manufacture was resumed from March 1st, 1882, however, solidification of the ore in the furnace occur on September 12, after 196 days of operation, and since the iron exit was closed by the harden ore, furnace operation stopped. Around this time vice head mining engineer ITO Yajiro came to Kamaishi, and investigated the deposits of ore. "General Report of Ministry of Engineering" was describing the result as follows.
The deposits of iron ore in mountains are about only 300,000t. And a half of this amount exist at difficult place by means of transportation. Furthermore, the quantity of trees for charcoal; drained also, can be supplied in about only two years. Therefore, the report, which assert that the iron mill should be abolish, was submitted to Ministry of Engineering. The engineer ADACHI Taro of the Kamaishi iron mill expressed the same opinion. Then, it determined to abolish the Kamaishi iron mill finally, and Ministry of Engineering also reported to the government.
By the investigation for deciding whether resumes or quit the big repair required blast furnace, it opted for abolition the iron-mill and it is in this opportunity since the amount for only two years are the deposit of iron ore stone. Now, the following four points are pointed out as the cause of failure of a national iron mill in "Survey Report on Kamaishi Iron Mine" by NORO Kageyoshi in February, 1893(4).
- Investigation of ore deposit was inadequate and the excavating area for the mine was very small.
- The area of the mountain where supplies the tree for charcoal was small.
- There was very little demand of iron at that time.
- The wages and prices of workers or oxen and horses soared very much.
Among these, Kurt NETTO who contributed greatly in respect of practice and education in the field of ore industry of Japan mentioned about above (3) in "Japan Mining"(5) which translated and summarized the transcript of lectures performed in the University of Tokyo in 1879, before the operation of the Kamaishi iron-mill started. In this book, iron demand in Japan was pointed out having not become at the time to materialize iron manufacture as industry.
If construction of road and bridges will be promoted from now on, the quantity of required iron will increase. Of course, if the enterprise for navy, shore protection of seashore is begun and/or railroad is laid newly, iron required quantity must be increase further. (omitted) Although there is an example, which is building the railroad between an iron ore mine and seashore now, on such a short distance railroad, it does not stand on the role to which iron demand is made to greatly increase.
It is a fact that transportation cost, personnel wages, etc. became 2 to 4 times by installation of so many national enterprise as described in above (4) in those days. However, even though the problem that resources were lost immediately, the iron mill was located along the seashore, therefore the iron ore stone supply from other areas was also possible. But, as NETTO had also made reference, since iron demand is still slight and there was no necessity for continues operation with immense deficit for the time, and the quit of the iron industry at Kamaishi was determined in Japanese government. As mentioned before, this project was done not by the private iron industry company (the quantity of output till then enough) or not the thing to depend on social, environmental request. That is, failure occurs, because the plan was carried out only by the reason said since it is a key industry in advanced nations while the prospect to the excavation of potential demand or demand had been opaque.
"Performance Report on Kamaishi Iron Mine" by KUWAHARA Masashi carried on Kougakusoushi vol.10 (August, 1882 issue, during second operation) has the next description about iron ore resources(6).
Investigation of the iron ore deposits of OHASHI mine was conducted by foreign employee GODFREY, BYANKHI and RYMAN, and each has submitted the report. However, neither is in what investigated the actual burying total amount only by presuming deposits with crop. Therefore, for Kamaishi iron mine, a required thing is prospecting investigation not only a mining enterprise but detailed now. By it, a total amount of ore should be presumed and future plans should be formed. However, it is that having begun a big enterprise like Kamaishi iron mill which is not clearly carried out the stage, cannot be believed, and engineers are just going to scorn such a case.
He has criticized severely like this. And said,
Furthermore, from newly investigation, if considered only without difficulty to extraction, it turns out that there is 100,000t in NIIYAMA and 120,000t crop deposits are in MOTOYAMA at least.
Even if continuous performance required 40t of ore per day, it is said that there are deposits for 15 years. Ore mining system of national iron mill term was open-cut mining, with blasting pulverization near the surface of the ground. The tunnel for mining was only dug dozens of meters for sampling. Moreover, nobody was performing presumption of exact amount of deposits. In spite of it, the iron-mill were abolished considering drain of iron ore as the greatest reason.
Furthermore, in NORO report, besides the above mentioned four points, has another description for abandon the operation of the furnace. This fact is not stated in the "General report of ministry of engineering".
The administrator of Kamaishi iron-mill predicted that expenditure exceeds the income and deficit increased increasingly with enterprise continuation by shortage of materials. Then, since raw ore which have not been pre-burned, and raw crude coke and coal, in order to reduce the cost of manufacture, were supplied to the blast furnace, therefore, solidification took place inside the furnace immediately. However, this can be said having only promoted discontinuance of iron mill and not the main reason of discontinuance.
It is being written in NORO report that the cause of solidification in the furnace at which became the cause of discontinuance of the iron mill, is because having excluded pre-burning of ore and having thrown in this raw ore in order to lessen deficit as much as possible, coke and coal of inferior quality were supplied to the blast furnace. As mentioned above, this blast furnace, although it was 60 percent of capability, continuously performed for 97 days until charcoal supply is lost in 1880. Therefore, it is not the main cause of the failure as said before that the internal form of the blast furnace was incongruent to the ore of Kamaishi area. Furthermore, description of engineer OSHIMA Yoshitaro who was working in the Tanaka iron mill, who purchased the national iron mill after operation failure, is different about the situation at this time in "Memorandum on meritorious of laced his lordship OHSHIMA Takato" which was written in 1921(7) (Figure 5).

Fig. 5 Memorandum on meritorious of laced his lordship OHSHIMA Takato(7).
Engineer ITO and foreign employee MORNIN came to Kamaishi for investigation of the deposits of the iron ore around the Ohashi area. (omitted) Seemingly, it was reported to Ministry of engineering that there was no hope, which can supply sufficient quantity of ore. This became the cause, and the Kamaishi iron mill bureau chief MOHRI and mining bureau chief SAEKI ordered to return to Ministry of engineering from Minister of engineering ITO. When ADACHI Taro served as the chief of Kamaishi mining bureau instead of these two persons, enterprise destruction was started and the raw ore about 5 inches cubic or more was made to throw in the 1st blast furnace, therefore, un-melting of ore occurs inside of the furnace and solidification occurs, and the 2nd blast furnace become the same condition. Therefore, discontinuance of business is decided, and not only officers but also all engineers were discharged and leave Kamaishi.
According to this document, investigation of ore deposits was carried out in parallel with second operation, and throwing of the raw ore is not for reduction of cost, and to have been conducted intentionally in order to interrupt an enterprise. According to the performance record of Nakaosaka iron-mill(8), the ore which was pre-burned and was crushed at the size of a fist and again crushed to the size of "about 1.5cm cubic" with the pulverization vessel, and having thrown it into the blast furnace in operation. Also in operation record of SYUSEIKAN (kagoshima), iron sand (crushed ore) was used for blast furnace. According to these records, the size of the ore thrown into a blast furnace was already established with the 1.5cm grade cubic at the last stage of Edo period in Japan. Therefore, "10 to 15cm cubic" in Kamaishi is 10 times the size of this, and using raw ore are thought that it must be done intentionally.
On the other hand, the "Survey report on ministry of engineering" raised before has the following description.
Although engaged in the work of the blast furnace for years, the foreign engineer never experienced such an accident. Although it was going to take various measures, neither took effect.
It turns out that a foreign engineer is without being able to solve the cause, slag solidified.
In June 1881, ADACHI Taro was transferred to Kamaishi, head officer MOHRI Motosuke leave Kamaishi in August, and in November ADACHI become the chief officer and he also become chief of accounts. Therefore, at the second operation he was the general chief of Kamaishi iron mill. If the raw ore, which is not pre-burned is thrown in the furnace, foreign engineers must be recognizes well that ore does not melt. Therefore, it is appropriate that the foreign engineers never direct to use raw ore, but chief officer ordered. And it is higher for validity to think that the political intention was there.
,S. Epilogue
It is difficult to conclude only by the above documents whether throwing in raw ore to the blast furnace is intentionally for the rash act for giving up the enterprise promptly or only considered financial retrenchment which originates ignorantly. However, the cause of abandonment of operation were the four points which NORO Kageyoshi pointed out, especially too little iron demand of those days.
With it being clear that the iron mill must be soon giving up by drain of resources (in fact incorrect information) as for the iron industry in Kamaishi at which a large amount of deficit was suffered, therefore only increase the deficit if the operation continued, and it have to quit the operation immediately, with avoid censure at insufficient preliminary investigation, it is simplest way to throw in raw ore in the furnace under operation, to make it blockade, and to make it physical failure. Although the blockade of a blast furnace was not the main factor as a cause of discontinuance of the enterprise, in order to advance discontinuance of business promptly, it was an incident with a big meaning.
Cause of the failure of national Kamaishi iron mill was the insufficiency of the preliminary survey including marketability, and the artificial thing made by the political intention. However, after this failure, industrialization of Japan progressed rapidly, and iron demand grew, so the Tanaka iron mill who received disposal of huge equipment in cheap amount of money, begun to operate the small size furnace same type as OSHIMA (Figure 6) in 1886, and finally, the former national 25t blast furnace started operation after reconstruction in 1894, so for this company, big initial risk was avoided. And in 1901 national Yahata Iron Mill began to operate, therefore iron industry become a key industry in Japan.
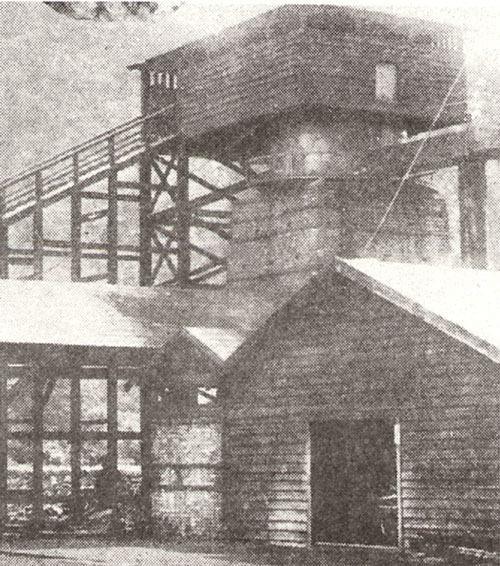
Fig. 6 Small size furnace same type as OHSHIMA.
The author acknowledges that this research was partly supported by Grant-in-Aid for Scientific Research on Priority Areas KAKENHI-14023201.
References (all in Japanese)
- Motoda, Y., Introduction of international technical cooperation, Morikita Press (1995).
- Onodera, H., Transformation of regional community with transfer of new technology, Proc. JSME annual meeting, 95-1-IV (1995), pp.383-384.
- Ministry of finance ed., Survey report on Ministry of Engineering (Reproduction), Hara-Syobo (1979).
- Noro, K. & Komura K., Survey report on Kamaishi iron mine(Reproduction) Japan Steel Kamaishi iron mill, (1986)
- Netto, K., Japan Mining, University of Tokio (1880).
- Kuwahara, M., Performance report on Kamaishi iron mine, Kogakusoushi, 10 (1882), p.489.
- Ohshima Y., Memorandum on meritorious of laced his lordship OHSHIMA Takato (Reproduction), Personal communication from Dr. Okada K. (1994).
- Osaka senior elementary school ed., Record of Osaka village, personal communication from Mr. Harada T. (1910).
|